半導体は3つの主要な工程を経て完成する
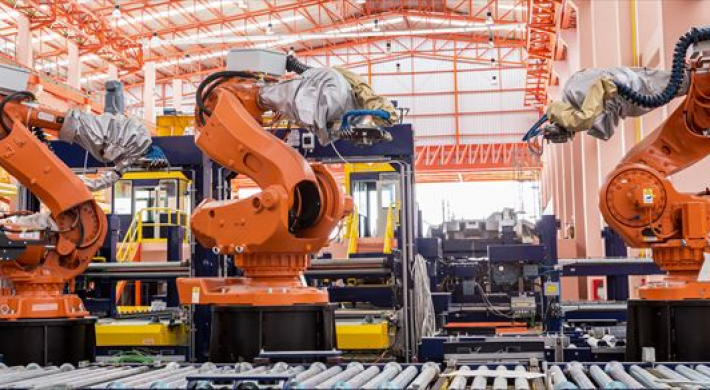
設計とウエハ作成から始まる工程
半導体製造の最初の工程は設計から始まります。
ここでは製品の用途に応じた回路設計が行われ、その後、フォトマスクと呼ばれる回路パターンを形成するためのテンプレートが作成されます。
その設計が完成したら、次に使うのがシリコンウエハです。
これは高純度のシリコンを円形にスライスしたもので、半導体のベースとなります。
続いて行われるのが前工程と呼ばれる作業です。
前工程ではウエハの表面を洗浄し、フォトリソグラフィによって回路を転写し、エッチングや成膜、イオン注入、平坦化といった複数の処理が順に行われます。
この段階では人の手による作業はほとんどなく、自動化された半導体製造装置が高い精度で各工程を進めていきます。
前工程が終わった時点で、ウエハの上には数百個以上のチップが形成されており、次の工程へと移行します。
最終工程で品質と性能を確認する
前工程が終了すると、次に行うのが後工程です。
ここではウエハ上に並んだ多数のチップを一つ一つ切り出し、それぞれをパッケージ化していく作業が行われます。
まずチップを切断するダイシングが行われ、次にチップを土台に固定し、ワイヤーボンディングで配線をつなぎます。
その後、外部からの衝撃や汚れからチップを守るためのパッケージングが施され、見た目にも完成品らしい形となります。
しかし、ここで終わりではありません。
完成した半導体は出荷前に厳しい検査を受けます。
検査では、動作に不具合がないか、仕様通りに性能が発揮されているかを詳細にチェックします。
この検査工程も非常に重要で、合格した製品のみが最終的に家電製品や車載機器として使用されるのです。
また、検査装置やパッケージング装置などもすべて半導体製造装置の一種であり、それぞれが高性能な機能を持っています。